Improving safety while reducing downtime – Pukekohe shows us how it’s done
Wednesday, 31 August, 2022
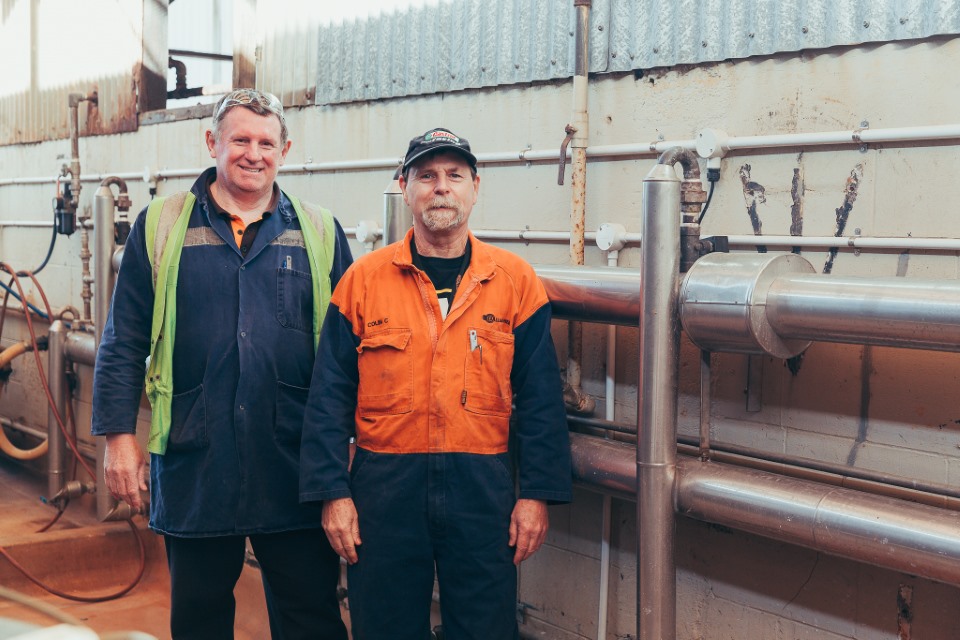
We love sharing the stories of our team members around the globe going above and beyond, enabling us to reach new heights. Recently, some of our Pukekohe-based team solved an ongoing issue of how to ensure a high standard of health and safety while reducing production downtime. We reached out to Business Unit Manager Ian Richards who shared more about what’s happened.
Pukekohe’s hot dip galvanizing plant undergoes regular repairs and maintenance to ensure the safety of our team and to keep the process running smoothly. The steam lines – which feed steam to the coils in the hot dip to keep the chemicals in the pre-treatment tanks hot – were originally located on a wall above the chemical pre-treatment tanks which kept them well out of reach of the hazardous chemicals used in the galvanizing process. This made sense from a health and safety perspective, but when the time came for repairs and maintenance, problems started to arise.
“The entire production line would be disrupted when we did scheduled maintenance. We would have to set up scaffolding to reach the steam lines, which cost both time and resources, and it was even more disruptive in the event of unplanned maintenance issues,” explained Ian.
Using continuous improvement, visual planning, and lean thinking (which are also key Better Ways of Working principles), a few of the engineering team, including Colin Crispe, Gary Potter, and Nathan Saunderson, got together to brainstorm options to reduce production downtime, while simultaneously ensuring a high level of health and safety.
They redesigned the pipeline so that it now runs at ground level on the other side of the wall. This means scaffolding is no longer required to access it, and the pipes are safely away from molten zinc, which Ian says sprays around a fair bit during the dipping process.
“The added benefit of getting the piping away from a corrosive environment also means it’s a lot better on the gear. The solenoid valves which help regulate the steam flow will now last much longer in their new area. Our engineers also brought the entire system down to a lower voltage (from 230 volts AC down to 24 DC), which is also a big safety improvement, while allowing the team to disconnect the wiring themselves – the lower voltage means the team doesn’t have to wait for an electrician to arrive. Another benefit is that maintenance can be done to the steam lines while the hot dip galvanizing plant is running.
You might be wondering, why go to all this effort now?
“It’s a progressive thing” explains Ian. “Our Health and Safety standards at Gallagher are constantly evolving – our needs have changed and developed over time, and the risks associated with our work in Pukekohe has driven us to think about what we can do to make our job safer, which in turn helps the production line.
“In the same way we moved away from using ladders to reach high places to using scaffolding, we’re actually removing the need for scaffolding all together by relocating our pipeline to ground level.”
This is a fantastic example of team members closest to a problem using continuous improvement to challenge old ideas and find better ways of working. Nice work Pukekohe!
Go back to Why Gallagher to find out more about us!