La collaboration est la clé pour répondre à la demande de produits
Wednesday, 27 July, 2022
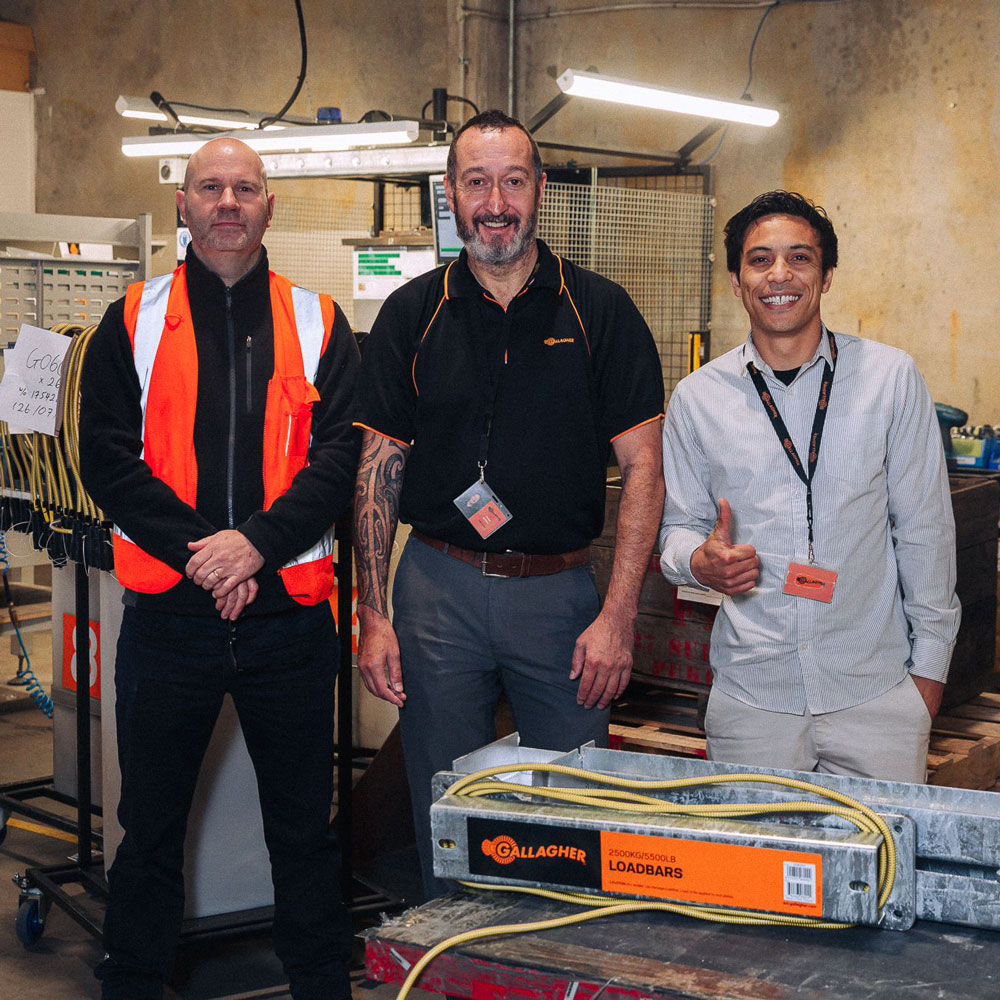
On n'associe généralement pas l'explosion des ventes à de mauvaises nouvelles, mais pour Animal Management, l'énorme succès de ses barres de charge sans fil a poussé notre équipe de production à se surmultiplier pour répondre à la demande. Cependant, dans la plus pure tradition Gallagher, certains membres de notre équipe se sont réunis pour étudier les moyens de prendre les devants, et nous avons rencontré quelques-uns d'entre eux pour voir ce qui s'est passé.
Shane Morell, responsable de la planification et des processus pour les opérations, explique que l'équipe s'est retrouvée dans une situation où la quantité de production de barres de charge finies ne correspondait pas à la demande du marché.
« Un groupe d'entre nous s'est réuni, comprenant la planification, l'approvisionnement, une partie de l'équipe de production, l'ingénierie et le développement de produits, afin de déterminer ce que nous pouvions faire pour améliorer la situation - il s'agissait d'une approche très transversale visant à déterminer comment nous pouvions augmenter notre production », explique Shane.
« Nous avons organisé une réunion de triage hebdomadaire au cours de laquelle tout le monde se réunissait, se fixait des objectifs et essayait de déterminer ce qu'il fallait faire pour augmenter les stocks à la sortie. Nous faisions régulièrement le point sur nos progrès et nous procédions à des tests et à des itérations. »
L'approche adoptée pour résoudre le problème est un excellent exemple de meilleures méthodes de travail, que l'équipe des opérations défend depuis un certain temps déjà, notamment grâce à son esprit d'amélioration continue, à la planification visuelle et à la pensée allégée.
Comme le souligne Kevin Holmes, responsable de la chaîne de valeur des plastiques, « les données historiques concernant les barres de charge sont les mêmes depuis une vingtaine d'années. Il n'y a jamais eu besoin de plus que ce qu'il y avait, mais presque instantanément, ils ont dit que nous avions besoin de 400 à 500 % de production en plus chaque jour pour répondre à la demande, et c'est donc ce que nous avons dû essayer de faire.
L'augmentation considérable de la demande est en fait double : la demande pour l'ancienne variante câblée a grimpé en flèche, tandis que l'intérêt pour la nouvelle barre de charge sans fil n'a cessé de croître depuis son lancement.
Jarrod Jones, responsable de la production de matières plastiques, explique que l'un des facteurs de ralentissement est le temps nécessaire au durcissement des cellules. « Les cellules de charge passent par des fours pour durcir, ce qui prend évidemment du temps, et les fours dont nous disposions ne nous permettaient de produire que 80 cellules par jour ».
Heureusement, l'équipe d'ingénieurs est tombée sur un très grand four pouvant contenir environ 400 cellules. Elle l'a donc acheté et a dû reconfigurer l'espace de production pour l'adapter - le hangar 7 de notre site d'Hamilton (où nous produisions à la fois des barres de charge et des capteurs de pesage) est désormais utilisé exclusivement pour les capteurs de pesage.
En fait, l'équipe a dû diviser ce qui était une opération en deux, ce qui signifie qu'elle a également dû augmenter les ressources nécessaires. En outre, de nombreux membres de l'équipe d'assemblage de matériel ont été formés pour pouvoir participer au nouveau processus. Ce qui était une équipe de trois personnes qui extrayaient 80 cellules par jour devient une équipe de 13 personnes qui en extraient 320 par jour !
Tout ne s'est pas déroulé sans heurts, explique Shane. « Nous avons été confrontés à des facteurs tels que la complexité du problème, qui signifiait qu'il fallait attendre jusqu'à trois mois pour voir des changements, le taux de rotation élevé au sein de l'équipe de production et les problèmes liés aux fournisseurs externes, qui ont tous causé un contretemps. Il y avait beaucoup de pièces en mouvement - Pukekohe était également impliqué, ainsi que nos fournisseurs externes de peinture en poudre ».
Mais malgré les difficultés, l'équipe a remporté une belle victoire. « Elle a très bien fonctionné. Nous n'avons pas été aussi rapides que nous l'aurions voulu, mais nous l'avons quand même été dans l'ensemble. L'ensemble de l'entreprise Gallagher nous a beaucoup soutenus ; ils ont compris la complexité de la situation et nous ont permis d'avancer à notre rythme, car nous n'aurions pas pu aller plus vite.
Bien que spécifique aux barres de charge, l'équipe estime qu'il y a beaucoup d'enseignements à tirer qui peuvent s'appliquer à de futurs changements. « Nous sommes parvenus à nous adapter à un rythme aussi rapide, et je pense que nous pourrons appliquer nos enseignements à d'autres domaines de la production si nous en avons besoin à l'avenir », déclare Shane.
« En tout, environ 25 personnes de tous les secteurs de l'entreprise ont participé à ce projet d'optimisation, et ce fut une expérience fantastique.
Shane Morell, responsable de la planification et des processus pour les opérations, explique que l'équipe s'est retrouvée dans une situation où la quantité de production de barres de charge finies ne correspondait pas à la demande du marché.
« Un groupe d'entre nous s'est réuni, comprenant la planification, l'approvisionnement, une partie de l'équipe de production, l'ingénierie et le développement de produits, afin de déterminer ce que nous pouvions faire pour améliorer la situation - il s'agissait d'une approche très transversale visant à déterminer comment nous pouvions augmenter notre production », explique Shane.
« Nous avons organisé une réunion de triage hebdomadaire au cours de laquelle tout le monde se réunissait, se fixait des objectifs et essayait de déterminer ce qu'il fallait faire pour augmenter les stocks à la sortie. Nous faisions régulièrement le point sur nos progrès et nous procédions à des tests et à des itérations. »
L'approche adoptée pour résoudre le problème est un excellent exemple de meilleures méthodes de travail, que l'équipe des opérations défend depuis un certain temps déjà, notamment grâce à son esprit d'amélioration continue, à la planification visuelle et à la pensée allégée.
Comme le souligne Kevin Holmes, responsable de la chaîne de valeur des plastiques, « les données historiques concernant les barres de charge sont les mêmes depuis une vingtaine d'années. Il n'y a jamais eu besoin de plus que ce qu'il y avait, mais presque instantanément, ils ont dit que nous avions besoin de 400 à 500 % de production en plus chaque jour pour répondre à la demande, et c'est donc ce que nous avons dû essayer de faire.
L'augmentation considérable de la demande est en fait double : la demande pour l'ancienne variante câblée a grimpé en flèche, tandis que l'intérêt pour la nouvelle barre de charge sans fil n'a cessé de croître depuis son lancement.
Jarrod Jones, responsable de la production de matières plastiques, explique que l'un des facteurs de ralentissement est le temps nécessaire au durcissement des cellules. « Les cellules de charge passent par des fours pour durcir, ce qui prend évidemment du temps, et les fours dont nous disposions ne nous permettaient de produire que 80 cellules par jour ».
Heureusement, l'équipe d'ingénieurs est tombée sur un très grand four pouvant contenir environ 400 cellules. Elle l'a donc acheté et a dû reconfigurer l'espace de production pour l'adapter - le hangar 7 de notre site d'Hamilton (où nous produisions à la fois des barres de charge et des capteurs de pesage) est désormais utilisé exclusivement pour les capteurs de pesage.
En fait, l'équipe a dû diviser ce qui était une opération en deux, ce qui signifie qu'elle a également dû augmenter les ressources nécessaires. En outre, de nombreux membres de l'équipe d'assemblage de matériel ont été formés pour pouvoir participer au nouveau processus. Ce qui était une équipe de trois personnes qui extrayaient 80 cellules par jour devient une équipe de 13 personnes qui en extraient 320 par jour !
Tout ne s'est pas déroulé sans heurts, explique Shane. « Nous avons été confrontés à des facteurs tels que la complexité du problème, qui signifiait qu'il fallait attendre jusqu'à trois mois pour voir des changements, le taux de rotation élevé au sein de l'équipe de production et les problèmes liés aux fournisseurs externes, qui ont tous causé un contretemps. Il y avait beaucoup de pièces en mouvement - Pukekohe était également impliqué, ainsi que nos fournisseurs externes de peinture en poudre ».
Mais malgré les difficultés, l'équipe a remporté une belle victoire. « Elle a très bien fonctionné. Nous n'avons pas été aussi rapides que nous l'aurions voulu, mais nous l'avons quand même été dans l'ensemble. L'ensemble de l'entreprise Gallagher nous a beaucoup soutenus ; ils ont compris la complexité de la situation et nous ont permis d'avancer à notre rythme, car nous n'aurions pas pu aller plus vite.
Bien que spécifique aux barres de charge, l'équipe estime qu'il y a beaucoup d'enseignements à tirer qui peuvent s'appliquer à de futurs changements. « Nous sommes parvenus à nous adapter à un rythme aussi rapide, et je pense que nous pourrons appliquer nos enseignements à d'autres domaines de la production si nous en avons besoin à l'avenir », déclare Shane.
« En tout, environ 25 personnes de tous les secteurs de l'entreprise ont participé à ce projet d'optimisation, et ce fut une expérience fantastique.